Influence of local microstructure on the formability of extruded composite profiles
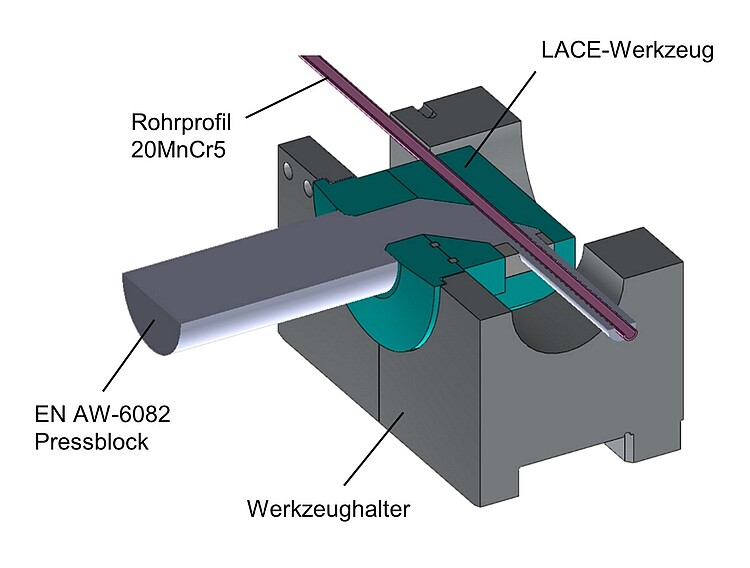
Year: | 2015 |
Date: | 30-06-19 |
Funding: | DFG |
Duration: | 07/2015 - 06/2019 |
Subproject A1 focuses on the development of a compound extrusion process which enables the continuous production of hollow profiles consisting of aluminum alloys and steel. The extruded profiles serve as a semi-finished product used in a subsequent forging process to produce bearing bushes (subproject B2), and therefore, they demand special properties. Besides the challenging process development, special focus is laid on sufficient weld seam properties and on the formation of continuous material bonding between aluminum and steel. The case-hardened steel (20MnCr5) acts as the wear-resistant functional surface of the bearing bushes. As seen in figure 1, the steel is inserted laterally as a tube into the modular extrusion die, especially designed so that the tube does not undergo deformation. The aluminum wrought alloy EN AW-6082 is then extruded onto the entire circumference of the steel profile via Lateral Angular Co-Extrusion (LACE). The quality of the metal bonding is determined first by the character of the bonding surface such as the presence of oxide layers and the creation of juvenile metallic surfaces during deformation, and second, by the intermetallic phases formed in the diffusion zone. The aim of this project is to investigate the influence of the interphase properties on the subsequent forging process and whether the bonding strength can be improved by process-dependent structural properties e.g. texture of the aluminum components, or the mechanical properties of the weld seam. The influence of the process parameters such as temperature, pressure, and time on the diffusion process in the bonding area will be examined accordingly in a deformation dilatometer. The results will be used for a numerical simulation of the process in a macroscopic model. The design of the extrusion process will be determined by means of numerical simulation, aiming at the formation of compound profiles with an adequate thin interphase suitable for the subsequent forming process. The joining zone of the extruded compounds will be analyzed using light and scanning electron microscopy techniques. The gained insights will be applied for the benefit of the process design and for the validation of the model.